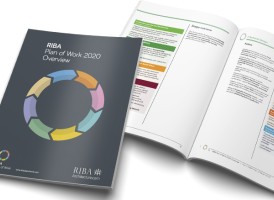
What the RIBA Plan of Work 2020 means for manufacturers
26 August 2020
The RIBA Plan of Work, first developed in 1963, has become the standard for organizing constructi...
17 September 2021 | By NBS
For manufacturers, getting your CPD RIBA-approved puts your products right in front of architects. These seven specification essentials are one of the key elements in securing approval.
All architects are required to do regular CPD to maintain their chartered status with RIBA. For manufacturers, this presents an opportunity to create RIBA-approved training materials around their products that architects will be eager to learn from at a crucial stage of their professional development.
NBS research in 2019 found that 60% of architects specify one or more of a manufacturer’s products after undergoing their RIBA CPD. With that in mind, it’s little surprise that the research also showed that 85% of RIBA Chartered members and 75% of non-members are familiar with the RIBA CPD Providers Network logo that indicates the CPD is RIBA-approved and choose it over other CPD. As a result, RIBA has the trust of our industry, and you can use that to your own advantage by delivering RIBA-approved CPDs.
There are several requirements that RIBA considers when they are assessing CPD materials. One of the key elements during the assessment is checking that the content covers the seven specification essentials. This is a requirement for all product specification CPD material. They are in place to ensure safe and informed specification and design. We’ve created this article to help you understand each specification essential, as though there are other factors that go into RIBA’s approval process, getting these elements right is a good start . You can provide information about these essentials as handouts, extra PDFs or a section in your main CPD material; it really depends on the product, the theme of the content, and the focus of the CPD .
All manufacturers’ CPD materials need to include or touch on necessary statutory and regulatory information that affect the products used in the CPD itself. To achieve this, check your product against the following current regulatory or statutory requirements and if required, detail in the CPD how it meets these fields:
● Building Regulations and associated approved documents.
● British Standards.
● EU Standards.
If you’re delivering your CPD as a seminar, you might be able to provide this information as a supplementary handout. This depends on the product and the focus of the CPD. However, significant information such as fire classification should be included in the main presentation.
All CPD materials must be designed to allow architects to make informed decisions on health and safety matters. As architects are often responsible for meeting the duties contained in the HSE’s Construction and Design Management Regulations 2015, your CPD materials should make it easy for an architect to identify risks, eliminate hazards and be informed of residual risks.
Examples of this include information on both how a product’s risks can be managed and how the installation requirements can be made safe. Think of how a large product could be transported safely to site, or how dust and other particles can be minimized if your product is cut. By including this information, you’ll not only meet RIBA’s expectations, but it will help an architect make safety-conscious decisions that will endear them to your brand and could even potentially avoid injuries or fatalities on site.
In an eco-conscious world, architects face more pressure than ever to design projects that are low-carbon, create minimal waste and maximize value to the client and society in general. To support members in their work towards better performance outcomes, the RIBA have created a series of guides on designing sustainable buildings, as well as updating the RIBA Plan of Work to embed and encourage sustainable design strategies at each work stage. The RIBA 2030 Climate Challenge sets out a series of targets for practices to adopt to reduce operational energy, embodied carbon and potable water.
As a CPD provider, that means you need to include as much information as you can about the sustainability of your products and how they meet or exceed the minimum standards set out in the regulatory compliance. This might include, for example, Approved Document H: Drainage and waste disposal, Approved Document Part L: Conservation of fuel and power, BREEAM and LEED.
Remember: you don’t need to make your whole CPD material about this, you can include much of this information in an additional way as outlined above. But knowing that RIBA wants sustainability information is a sure sign of the future of our industry. If you have yet to assess the carbon credentials of your products and business, it could be a good way to showcase your business’s CSR practices.
Inclusive environments are places that work better for everybody – whether that place is a school, office, park, street, care home, bus route or train station. Inclusive environments make places and spaces that reflect the diversity of people who want to use them.
Access to buildings and services is enshrined in law by the Equality Act 2010 and associated statutory instruments. Your CPD materials should include details around the inclusivity or access considerations for materials or products you provide when they will be used in projects, so that architects can assess whether they will be suitable for their projects. This means considering several things, for example physical, visual and aural impairment, but also wider inclusion and access issues.
Depending on the theme of the content, any information provided in this section should be considered against the common British legislative documents which cover inclusive design:
Whenever you can, give information out that helps learners comprehend the suitability of your products. This could include things like your product’s scope of application or information that helps show the consequences of improper installation or application. For example, if a learner was to use different fixings or adhesives, would that compromise the finished ‘build’? If so, your CPD should make this clear.
Basically, you should design your CPD materials to show the best and most correct application/ installation and use of your products. You might also detail any issues where a product may ‘appear’ suitable for something but is not, such as if you offer an anti-slip tile that is only suitable for floor usage in specific circumstances.
By being clear about how your products should be used, and when they are dependent on correct detailing and reliant on other products, you can help avoid them being misused by architects in the design stage and by construction workers on site.
What are the long-term maintenance requirements of the material and/ or products that designers need to consider? This information will inform delegates’ design and specification decisions, including factors relating to, for example, maintenance issues, residual risks, cost of application vs cost of maintenance and additional design considerations.
In keeping with our point on sustainability, modern construction projects should be built around longevity to minimize their environmental impact. This also means maintenance is more important than ever, so learners must be equipped with all the necessary knowledge they need around your product’s maintenance cycle. If you need an example of how this works, consider a product that can be hidden out of sight for the end user in a space like a ceiling void. In this instance, the architect must design a way for maintenance teams to access the product when necessary, and how that access will impact their design. By including this kind of information in your CPD material, you’ll not only improve your chances of RIBA approval but also help persuade architects that your product, when installed using the learning from your CPD, is the most suitable and reliable choice for their designs.
There are few issues as critical to the construction industry as fire safety, especially following changes to the Building Regulations 2018, which prohibit combustible materials used as attachments to external walls in relevant buildings above 18 m.
Fire safety captures a wide design perspective, from an outline fire strategy plan to the reliance upon accurate, robust and appropriate selection and specification of products. However, in this context we expect all CPD material to address the issues of testing and combustibility (including the classification of materials), fire performance characteristics of materials (smoke production, flaming droplets and toxicity), appropriateness for purpose (including height), correct specification and system components.
As a manufacturer, your CPD must include clear and unambiguous technical information around the fire safety of your materials and products. Depending on the product, this should be part of the main CPD material and not as additional information.
You can look at and refer to RIBA’s fire safety resources.
Issues might include:
By following each point above, you’ll have taken care of one important aspect for RIBA approval. While there are other criteria to be included and assessed such as the learning material itself, providing these specification essentials is an important step.
Don’t forget that CPDs are also an opportunity to add value to an architect’s learning journey. As a member of the RIBA CPD Providers Network, you have exclusive access to standards, guidance and events that will help you get your CPD approved more quickly and create content that helps architects and others specify safely and smartly.
Open new doors to architects, have the chance to get your products specified into a project at an early stage, and win orders by delivering RIBA-approved CPD – become a member of the RIBA CPD Providers’ Network today. Click here to get started.