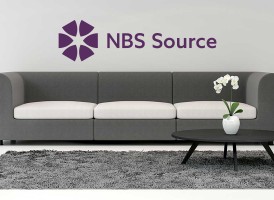
NBS Source & NBS Chorus - one connected solution
15 July 2021
NBS has been placing manufacturer’s products, systems and materials in front of specifiers since ...
30 March 2017 | By NBS
Following the launch of What Specifiers Want 2017, we asked four specifiers from a variety of practices, to share their experiences of specification, product selection and manufacturer support.
Nigel Wright (Architect and Director, Wright Class Solutions Limited)
Nigel is a chartered Architect, registered RIBA Client Adviser, an associate member of the Association for Project Management, a registered Design Quality Facilitator with the CIC, a Built Environment Expert with Design Council/CABE, and a Director at Wright Class Solutions: a company that he founded in 2012.
Their business mission is to create and inspire transformational value driven design solutions in the education, faith and community environments
Nigel helps his clients with their strategic definition and brief, and guides them through the design process to reveal opportunities for design quality to add value.
John Carpenter (Associate, Allies and Morrison)
John is a member of the Technical Team and the associate at Allies & Morrison responsible for the office specification: its production, content, maintenance and upkeep.
He provides technical guidance, research and support across most construction areas focusing on sustainability, responsible sourcing, environmental performance, materials and certification.
Laura Mansel-Thomas (Partner, Engineering, Ingleton Wood LLP)
Laura is a chartered engineer, MEI and MCIBSE, and manages a team of 30 M&E engineers and six sustainability specialists across five offices.
Recent projects have included The Shed, the hugely successful naturally ventilated theatre in central London. Her personal interest is in coordinated sustainable building design across all sectors. Her team of engineers has skills across all sectors, working for end user clients, architect-led design teams, contractors and as part of a multidisciplinar offering by Ingleton Wood.
They have particular strengths in education, healthcare, residential and cultural schemes.
Sally-Anne Balmer is an Architect and Chartered Member of the RIBA. The majority of her experience has been gained as Associate Architect at multi-disciplinary practice Bradshaw Gass and Hope, based in the North West.
She had responsibility for delivering projects across a variety of sectors, namely Conservation, Educational, Ecclesiastical, Leisure and Commercial. Two of her projects received multiple awards in 2012 and 2013: ‘The Space’ for charity group 42nd Street in Manchester and Trinity Methodist Church in Ellesmere Port. A move to the North East led to Sally-Anne setting up her own limited company, offering architectural consultancy services to both public and private clients, before joining the NBS as a Technical Author researching and writing content for NBS’s specification tools.
Nigel Wright
Architect and Director,Wright Class Solutions Limited
Design could be described as preparing a plan for change in response to a ‘Client Requirement’. Specification, a crucial aspect of the plan for change, is the act of identifying something precisely, or of stating a precise requirement. This involves a detailed description of the design, materials and the like, and how it should be done in order to make something of use. Personally, I believe the iterative process of preparing a specification should be undertaken with care, diligence, thorough research, foresight, and should be evidence-based. Decisions on choices of product and material should be socially responsible.
Assuring ‘Client Requirement’ compliance without a clear specification significantly increases the risk of failure, with the possibility of financial and environmental penalties and ultimately reputational damage. Unresolved matters of prescription, description, suitability, scope, context, sufficiency, technical compliance, performance, cost, maintenance, operation, dependency, concurrency, longevity, sustainability, well-being, recycling, reuse and disposal can remain at large, exposing the specification to uncertainty, ambiguity and misinterpretation.
When the documentation is put out to the market, most specifiers experience a dilemma. Tender returns often do not reveal sufficient information to safeguard prior decisions in matters of specification and compliance, or where there is reliance upon the tender to complete crucial elements of the design. Causes of change such as product substitution, lack of stock, programme limitations and manufacturers withdrawing or discontinuing products can be testing, and risk delivery to the ‘Client Requirement’ through to completion and into operation.
To assist the specifier, computer software technology and collaborative practice tools and techniques aim to promote faster, more accurate access to data, common standards, legislation and market product. Is this sufficient information for the building owner and their Facilities Management providers to manage their estate? In future, I believe product identification such as electronic product signature (Product DNA) and operational performance feedback may be required information for specifiers, building owners, and their Facilities Management practitioners.
“Causes of change such as product substitution, lack of stock, programme limitations and manufacturers withdrawing or discontinuing products can be testing”
John Carpenter
Associate, Allies & Morrison
Allies and Morrison have developed an approach for writing specifications based on ‘systems’: either ‘descriptively’ with attributes based on aesthetics and behaviour in use, or ‘prescriptively’ where these are more traditionally stated using prescriptions of form, methods of construction or materials used.
Systems can range from a single product, to a number of products contributing to a single unified item, to a build-up of separately supplied products and materials brought together to form a purpose-made or bespoke item or element for building into the works. However supplied, systems will always include information that allows for safe installation and correct interface with the adjoining systems to ensure that overall system performance is as intended. Crucially, it will be procured, manufactured, assembled, installed and, where applicable, warranted under a single point of responsibility, be that a specialist supplier, a certified installer or trade sub-contractor. If items or layers are not grouped together to form systems, performance cannot be properly identified; for example, the performance of a wall can only be specified as the complete build-up.
Elementally structured work packages bundled together and let to a single specialist supplier, certified installer or trade sub-contractor allow the detail design to be completed by a specialist who will have the knowledge, expertise and experience to complete the design, procure and assemble the components, deliver and finally install and warrant the completed installation. Many clients see the benefit of this, encouraging creativity and innovation in the supply chain, with the result that we find more technologically appropriate and sustainable solutions get to be used in many instances.
“If items or layers are not grouped together to form systems, performance cannot be properly identified”
Laura Mansel-Thomas
Partner, Engineering, Ingleton Wood LLP
Manufacturers’ information is not just about getting the details right in a specification. In my role, designing a well-coordinated building requires thinking very early in the project about plant spaces and riser sizes. In order to do this, we need to get manufacturers’ input without being able to guarantee that they will feature in the resultant specification. One particular air handling unit supplier has a reputation for quick, accurate information – and this is like gold dust. I have had a situation when, in the middle of a design team meeting, the architect suggested two triangular plant spaces to serve an auditorium. We knew the air change rate and rough cooling loads. The manufacturer’s representative was able to turn around a plant specification in under half an hour, so that, by the end of the meeting, we could confirm that the plant spaces were acceptable. This results in a saving in design time for the whole team (waiting a matter of days for confirmation would have held up the entire process) and a maximisation of usable area in the auditorium (as the alternative would have been to oversize the plant room). The manufacturer also knows that they are likely to get the eventual commission (which they did) as the Contractor won’t want to risk proposing a change in specification in such a tight space.
“Manufacturers’ information is not just about getting the details right in a specification”
Sally-Anne Balmer
Architect and Technical Author, NBS
(Former Associate Architect with Bradshaw Gass and Hope LLP (Construction Design Consultants)
When considering appropriate product solutions for their designs, discussions with manufacturers early on in a project can be of significant help to specifiers. On my own projects, it has been particularly useful when manufacturers offer an array of product options which enable different solutions to be considered. For example, when developing plans for a recent office development, which consisted of several connecting blocks with a variety of roof heights and pitches, no single roofing solution was appropriate. I contacted a manufacturer for further advice and explained the performance requirements that the various roof sections needed to achieve, in line with the aesthetic intent of the design. The resulting face-to-face discussions contributed significantly to establish which solutions were appropriate and achievable, before any time had been expended specifying incorrectly at the detailed design stage.
Some specifiers are reluctant to contact manufacturers, concerned that they will receive the ‘hard sell’ and get pressured into including proprietary product references in their specifications. This is, unfortunately, sometimes the case. However, if the specifier is clear from the outset on performance requirements and has carried out effective product research, then the good manufacturer will provide supporting technical advice on appropriate product selection. No one knows their products better than the people actually making them. It is invaluable for specifiers to be able to tap into this knowledge to contribute to the creation of an informed and up-to-date specification.
“On my own projects, it has been particularly useful when manufacturers offer an array of product options which enable different solutions to be considered”