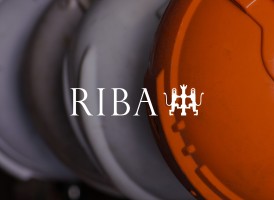
Manufacturers, RIBA CPD and the RIBA health and safety test
17 August 2021
Find out more about the health and safety test that the RIBA has just launched and the opportunit...
13 February 2024 | By David Bain and Allan Wilen
Modern Methods of Construction (MMC) can have a broad meaning, with a wide range of associated terms and definitions. In the National Audit Office’s 2005 report 'Using modern methods of construction to build homes more quickly and efficiently', MMC is defined by the Office of the Deputy Prime Minister as simply ‘…a process to produce more, better quality homes in less time’.
‘Modern Methods of Construction (MMC)’ can have a broad meaning, with a wide range of associated terms and definitions. In the National Audit Office’s 2005 report 'Using modern methods of construction to build homes more quickly and efficiently', MMC is defined by the Office of the Deputy Prime Minister as simply ‘…a process to produce more, better quality homes in less time’.1
It is sometimes seen as an umbrella term for the departure from traditional construction methods. The majority of products and materials have traditionally been constructed on site. MMC includes approaches where elements are assembled off site, in factory conditions, before being installed on site. Some approaches to construction that fall under the MMC umbrella have been around for some time. For instance, there were modular corrugated iron and horticultural buildings in the 1800s, and prefabricated housing in the second half of the 20th century.
The theory is that MMC can improve efficiency, reduce waste, improve customer satisfaction, achieve better environmental performance and provide more predictability with timescales. Terms associated with MMC include:
To provide some clarity, in 2019 the MHCLG2 Joint Industry Working Group on MMC (compromising Buildoffsite, Homes England, NHBC and RICS) created a seven-category definition framework for MMC.3
The UK Government has encouraged MMC. For instance, in its 2017 Autumn Budget, it said that government departments would favour off-site construction approaches in their capital programmes. The Conservative Party pledged support for MMC in its 2019 manifesto, and it features in its ‘Construction Playbook’.
Influential reports (such as Sir John Egan’s 'Rethinking Construction' and Mark Farmer’s 'Modernise or Die') have highlighted MMC and off-site construction methods as having the potential to solve some of the industry’s long-term problems, such as inefficiency and a shortage of housing.
The National House Building Council (NHBC) has provided information and guidance to support the use of more innovative approaches, like MMC, to increase the volume of home supply in the UK. And the Government has announced a new, larger £11.5 bn Affordable Homes Programme 2021-26 (AHP)4, including funding for social rent, supported housing and a renewed commitment to delivering homes using MMC.
So, has the support for MMC resulted in more projects using this approach?
According to Glenigan, there has been a gradual rise in the proportion of projects utilizing MMC approaches. Around 9% of new-build projects starting in 2017 employed MMC in some way. This rose to a high of 17% in late 2022, with the latest figures at 16% in 2023. Growth has fluctuated, but the overall trend is clearly upwards.
Off-site construction can, perhaps, be viewed as a more defined and easily understood approach, and as a subset of the broader MMC concept (which involves wider processes and methods).
‘Off-site construction can be simply defined as the part of the construction process that is carried out away from the building site. This can be in a factory or sometimes in specially created temporary production facilities close to the construction site (or field factories)’5.
There are different types of off-site construction, which include:
NHBC outlines similar categories in its guide to MMC.6
Looking at Glenigan data, we can see that the take-up of off-site construction, as a subset of MMC, has been especially strong for new-build projects. It was utilized in 7% of new-build projects started during the first nine months of 2023. By value, the proportion is higher (11%), reflecting the prevalence of off-site construction or manufacture on higher value projects.
While there is a lot of focus on how off-site can help solve the housing crisis, off-site construction or manufacture has made the greatest inroads into other sectors. The proportion of new starts that included some off-site elements were highest in industrial (29%), education (15%) and hotel and leisure (11%). The numbers are higher for new builds; for example, over 22% of new-build education projects included an element of off-site. The Department for Education has established an off-site framework for school buildings.7
In the 2023 NBS Digital Construction Report, we found that 57% of respondents had been part of a project that involved an element of off-site construction. This is an increase from 50% in our 2021 survey, reflecting the increase in adoption of off-site, evident in the Glenigan data. For consultants (such as architects and engineers), the figure was 58%, and it was 63% for contractors.
Drilling down, the most common type of off-site construction was for sub-assemblies and accessories. This is a broad category, potentially comprising any set of components made in a factory and brought to site. It can include many components, such as fairly large elements like roof trusses, staircases, door sets, precast concrete beams and prefabricated dormers. It can also include small components, which may not be readily associated with off-site construction, such as door locks and handles. The use of sub-assemblies may be taking place alongside traditional construction methods.
The other forms of off-site construction involve more substantial parts of a building or asset. These range from flat-packed panels, such as structural insulated panels (SIPS); for example, insulation between timber panels. Panelized systems can be timber-framed or steel-framed. These systems can include services like electrical sockets and water feed pipes. Over half of the survey respondents (52%) told us that they were involved in projects using panelized systems.
Just under a third (28%) of professionals responding to our survey were involved in projects using volumetric pod construction. They are partly assembled into three-dimensional rooms before leaving the factory, and are sometimes combined with panels (such as bathrooms used in hotels, for instance, or kitchens). This kind of hybrid approach was cited by 22% of our survey respondents.
Finally, modular construction (where large sections of the building are constructed into entire building modules) was utilized on projects by 34% of survey respondents. These include projects like blocks of flats or schools that consist of identical substructures manufactured as modules. There are a number of examples of residential buildings in the UK, such as Greenford Quay in London.89
If we exclude survey respondents that were only involved in projects using sub-assemblies and accessories, the proportion involved in projects using panelized or modular construction was 45%.
There have been some setbacks to MMC, with the closure of some modular factories, and housebuilders going into administration.10 One of the reasons for these closures is the lack of stability in the construction market, with fluctuations in demand. Regulations and standards relating to MMC and off-site construction are also limited – although there has been activity to address this, with BSI carrying out a review of related standards.11 Some of these challenges were highlighted in the recent inquiry by the House of Lord’s Built Environment Committee, which pointed to issues with the government’s approach to MMC.12 However, the inquiry recognized the MMC successes evident elsewhere – in housebuilding outside the UK, and in non-residential UK buildings.
Despite these challenges, the signs are that MMC and off-site construction will continue to see further growth. According to Glenigan, nearly 9% of new-build projects securing detailed planning approval during the first nine months of 2023 involved an off-site element. Strikingly a number of leading housebuilders have invested in their own off-site facilities; such vertical integration may provide a base level of demand for the manufacturing operations, reducing exposure to volatile market conditions.
In addition, economic, regulatory and environmental performance issues are set to encourage further growth in the use of off-site construction or manufacture over the medium term. The shortages of skilled labour are likely to intensify as the construction industry emerges from the current market downturn. The Building Safety Act is also set to change how projects are delivered, requiring more detailed pre-construction design and limiting the scope for on-site design changes. This should increase the opportunity for off-site components and systems. Clients and designers desiring to improve their buildings’ environmental performance are similarly likely to favour the greater use of off-site systems.
The statistics relating to the adoption of MMC and off-site construction in this article are from the NBS Digital Construction Report 2023, and from the Glenigan project database. Read more about the construction industry’s adoption of digital technologies and methods in the NBS Digital Construction Report 2023. And you can read Glenigan’s expert insight and commentary on the UK construction market, including the Glenigan Forecast.
1. https://www.nao.org.uk/wp-content/uploads/2005/11/mmc.pdf
2. https://www.gov.uk/government/organisations/department-for-levelling-up-housing-and-communities
3. https://www.gov.uk/government/publications/modern-methods-of-construction-working-group-developing-a-definition-framework
4. https://www.housing.org.uk/link/9e36ccf90a0d4d05908067f27be3d1fa.aspx
5. https://www.buildoffsite.com/content/uploads/2016/01/OffsiteGuide.pdf (page 10)
6. https://www.nhbc.co.uk/foundation/a-guide-to-modern-methods-of-construction
7. https://www.gov.uk/government/publications/offsite-construction-framework-modern-methods-of-construction/modern-methods-of-construction-mmc1
8. https://www.egi.co.uk/news/is-volumetric-the-future-for-housing-development
9. https://www.hta.co.uk/project/greenford-quay
10. https://www.building.co.uk/news/government-cant-subsidise-mmc-forever-warns-housing-minister/5126831.article
11. https://www.buildoffsite.com/content/uploads/2019/04/BSI-report.pdf
12. https://www.architectsjournal.co.uk/news/governments-modular-construction-strategy-in-disarray-inquiry-warns